I. Introduction
In the intricate world of textiles, where innovation constantly reshapes what's possible, few materials have had as profound an impact as synthetic yarns. From the clothes we wear to the furnishings in our homes, these engineered fibers offer a blend of performance and aesthetics that natural fibers often cannot match. Among them, Drawn Textured Yarn (DTY) stands out as a true workhorse, revolutionizing comfort, durability, and design in countless applications.
DTY, short for Drawn Textured Yarn, is a type of synthetic filament yarn that has undergone a specialized texturizing process. Unlike flat, smooth filament yarns, DTY is characterized by its bulk, elasticity, and soft, natural hand feel, often mimicking the comfort of cotton while retaining the superior performance of synthetics. Its significance in the textile industry cannot be overstated; DTY offers unparalleled versatility, enabling manufacturers to create fabrics that are not only comfortable and aesthetically pleasing but also highly functional and cost-effective. This article will delve into the fascinating world of DTY yarn, exploring its definition, manufacturing process, various types, key advantages, diverse applications, and the exciting future trends shaping its evolution.
DTY yarn is a synthetic filament yarn that has been processed to impart bulk, stretch, and a softer texture. The term "Drawn Textured Yarn" precisely describes its creation:
-
Drawn:
This refers to the initial stretching of the synthetic filaments. During this stage, the partially oriented yarn (POY) is stretched to align its molecular structure, significantly increasing its strength and tenacity. This drawing process is crucial for the yarn's subsequent performance.
-
Textured:
After drawing, the yarn undergoes a texturizing process. This involves introducing permanent crimps, loops, or coils into the continuous filaments. This mechanical alteration gives the yarn its characteristic bulk, elasticity, and a more natural, less synthetic feel. The most common method for DTY is false-twist texturizing.
Primarily made from synthetic polymers like Polyester and Nylon, DTY yarn possesses a unique combination of characteristics that make it highly desirable:
- Soft and Comfortable Feel: One of DTY's most notable attributes is its soft, often cotton-like touch, which enhances wearer comfort.
- Good Elasticity and Stretch: The texturizing process imparts excellent stretch and recovery properties, making it ideal for activewear and comfortable garments.
- High Bulk and Cover: The added volume provides good fabric coverage and a fuller appearance.
- Good Drape and Wrinkle Resistance: DTY fabrics tend to drape well and resist creasing, maintaining a neat appearance.
- Excellent Color Fastness: Synthetic fibers generally hold dye well, and DTY is no exception, ensuring vibrant and long-lasting colors.
- Breathability: While synthetic, the textured structure allows for better air circulation compared to flat filament yarns, contributing to improved comfort.
III. The Manufacturing Process of DTY Yarn
The production of DTY yarn is a sophisticated multi-stage process that transforms polymer chips into high-performance textile fibers.
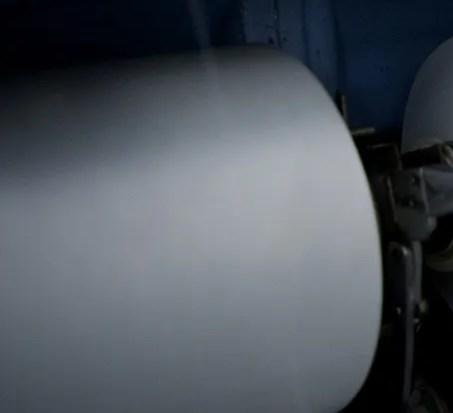
A. Raw Materials:
The primary raw materials used for DTY yarn are synthetic polymers:
- Polyester: By far the most common polymer for DTY due to its excellent strength, resilience, and cost-effectiveness.
- Nylon: Also used, offering superior elasticity and abrasion resistance, often found in hosiery and specialized activewear.
- Other Synthetic Polymers: While less common, other polymers may be used for specific niche applications.
B. Stages of Production:
-
Spinning (POY Production):
The process begins with the melt spinning of polymer chips. The polymer is melted and extruded through a spinneret (a plate with fine holes) to form continuous filaments. These filaments are then rapidly cooled and wound onto bobbins, resulting in Partially Oriented Yarn (POY). POY is characterized by its low orientation (molecules are not fully aligned) and high stretchability, making it suitable for further processing.
-
Drawing and Texturizing:
This is the core stage where POY is transformed into DTY.
- Drawing: The POY is stretched over heated rollers. This stretching process, known as drawing, aligns the polymer molecules along the fiber axis, significantly increasing the yarn's tensile strength, tenacity, and dimensional stability.
- Texturizing: Immediately following drawing, the yarn undergoes texturizing to introduce bulk and stretch. The most prevalent method for DTY is False-Twist Texturizing. In this process, the yarn is twisted, heat-set (to make the twist permanent), and then untwisted. Although the twist is removed, the heat-setting causes the individual filaments to retain a latent crimp or coil, giving the yarn its textured properties. Other less common texturizing methods include air-jet texturizing (using high-pressure air to entangle filaments) or knit-de-knit texturizing.
-
Heat Setting:
After texturizing, the yarn is subjected to a final heat-setting process. This stabilizes the newly imparted texture and dimensions, ensuring that the crimps and coils are permanent and the yarn retains its desired properties throughout subsequent textile processes and end-use.
-
Winding:
The finished DTY yarn is then precisely wound onto cones or packages, ready for shipment to weaving, knitting, or other textile manufacturing facilities.
C. Quality Control Aspects:
Throughout the manufacturing process, stringent quality control measures are applied to ensure consistent yarn properties, including tension, denier (yarn thickness), evenness, and strength.
IV. Types and Variations of DTY Yarn
DTY yarn is incredibly versatile, available in numerous variations tailored for specific applications and desired fabric characteristics. These variations are primarily based on raw material, luster, cross-section, and intermingling.
A. Based on Raw Material:
- Polyester DTY: The most common type, offering excellent strength, wrinkle resistance, and color retention.
- Nylon DTY: Known for its superior elasticity, abrasion resistance, and soft hand, often used in hosiery and performance wear.
B. Based on Luster:
The luster of DTY yarn is determined by the type and amount of delustering agent (e.g., titanium dioxide) added during polymerization.
- Semi-Dull (SD): The most common luster, offering a moderate sheen.
- Bright (BR): Has a higher sheen due to minimal or no delustering agent.
- Full Dull (FD): Has a matte, non-shiny appearance, often preferred for a more natural look.
C. Based on Cross-Section:
The shape of the filament's cross-section influences the yarn's luster, hand, and wicking properties.
- Round: The standard circular cross-section.
- Trilobal: A three-lobed cross-section that enhances luster and provides a silk-like sheen.
- Hollow: Filaments with a hollow core, offering improved insulation and lighter weight.
D. Based on Intermingling:
Intermingling refers to the process of entangling individual filaments within the yarn using air jets. This affects yarn cohesion and processing efficiency.
- Non-Intermingled (NIM): Filaments are not entangled, resulting in a very open, soft yarn.
- Slightly Intermingled (SIM): A low level of entanglement, offering some cohesion while maintaining softness.
- Highly Intermingled (HIM): Significant entanglement, providing high cohesion, reducing filament breakage, and making the yarn easier to process in weaving and knitting.
E. Other Specialized DTYs:
- Cationic Dyeable DTY: Modified polyester yarn that can be dyed with cationic dyes, allowing for brighter colors and cross-dyeing effects.
- Recycled DTY (RPET DTY): Made from recycled plastic bottles, promoting sustainability.
- Microfilament DTY: Yarns composed of extremely fine individual filaments, resulting in an exceptionally soft, luxurious hand feel and enhanced drape.
V. Advantages of DTY Yarn
DTY yarn's unique combination of properties provides a multitude of advantages that have cemented its position as a cornerstone of the modern textile industry.
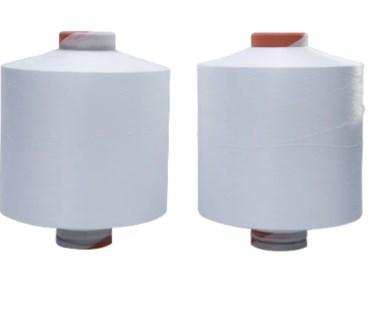
A. Comfort and Aesthetics:
- Soft Hand: The textured nature gives DTY a soft, pleasant feel against the skin, often comparable to natural fibers like cotton.
- Good Drape: Fabrics made from DTY exhibit excellent drape, allowing them to flow gracefully and conform well to the body.
- Natural Look: Especially with full dull lusters, DTY can mimic the appearance of spun yarns, offering a more natural aesthetic than flat synthetics.
B. Performance:
- Excellent Elasticity and Recovery: The inherent crimp provides significant stretch and excellent recovery, making it ideal for form-fitting garments and activewear that require freedom of movement.
- Good Moisture Management (Wicking Properties): The textured surface and inter-filament spaces can facilitate moisture wicking, drawing sweat away from the body and enhancing comfort during physical activity.
- Wrinkle Resistance: DTY fabrics are highly resistant to wrinkling, maintaining a smooth appearance even after prolonged wear or packing.
- Durability and Abrasion Resistance: Synthetic polymers are inherently strong, and DTY retains this durability, offering good resistance to wear and tear.
- Easy Care: DTY fabrics are typically quick-drying and require minimal ironing, making them convenient for modern lifestyles.
- Color Fastness: DTY yarns exhibit excellent color fastness, meaning colors remain vibrant and resist fading even after repeated washing and exposure.
C. Versatility:
The wide range of deniers, lusters, and intermingling options makes DTY suitable for an incredibly diverse array of applications, from delicate innerwear to robust upholstery.
D. Cost-Effectiveness:
Compared to certain natural fibers, especially when considering durability and performance over time, DTY often offers a more cost-effective solution for large-scale textile production.
VI. Applications of DTY Yarn
The versatility and performance benefits of DTY yarn have led to its widespread adoption across numerous sectors of the textile industry.
A. Apparel:
DTY is a dominant yarn in the apparel sector due to its comfort, stretch, and easy-care properties.
- Sportswear and Activewear: Leggings, tracksuits, jerseys, yoga pants, and athletic tops benefit from DTY's elasticity, moisture-wicking, and durability.
- Casual Wear: T-shirts, dresses, skirts, and blouses often incorporate DTY for comfort, wrinkle resistance, and soft hand.
- Innerwear and Lingerie: Its softness and stretch make it ideal for intimate apparel.
- Hosiery and Socks: DTY provides the necessary stretch and comfort for various types of hosiery.
- Denim: Used as a stretch component in stretch denim to provide comfort and shape retention.
- Outerwear: Jackets, windbreakers, and other light outerwear can utilize DTY for its resilience and quick-drying properties.
B. Home Textiles:
DTY's durability and aesthetic versatility make it suitable for various home furnishing applications.
- Upholstery Fabrics: Used in furniture upholstery for its durability, resistance to abrasion, and ability to mimic natural textures.
- Curtains and Drapes: Provides good drape, color fastness, and resistance to sunlight degradation.
- Bedding: Sheets, duvet covers, and pillowcases benefit from DTY's softness, easy care, and wrinkle resistance.
- Carpets and Rugs: Used in certain types of carpets for its resilience and wear resistance.
C. Industrial Textiles:
While less common than in apparel, DTY finds applications where its specific properties are advantageous.
- Automotive Interiors: Used in seat fabrics and other interior components for durability and aesthetic appeal.
- Bags and Luggage: Provides strength and abrasion resistance for various types of bags.
- Narrow Fabrics: Ribbons, webbings, and elastic bands often incorporate DTY for their functional properties.
D. Other Niche Applications:
DTY can also be found in specialized textiles like medical textiles, protective wear, and even some technical fabrics.
VII. DTY Yarn vs. Other Yarn Types (Brief Comparison)
Understanding DTY's unique position in the textile landscape is best achieved by comparing it to other common yarn types.
A. DTY vs. FDY (Fully Drawn Yarn):
- FDY: A flat, smooth, continuous filament yarn. It has high strength and luster but lacks bulk and stretch. Used where smoothness and sheen are desired (e.g., linings, certain apparel).
- DTY: Textured, bulky, and elastic. Offers a soft hand and better coverage. More comfortable for next-to-skin applications.
B. DTY vs. POY (Partially Oriented Yarn):
- POY: The intermediate product in DTY manufacturing. It is only partially drawn, making it less stable and strong than DTY. POY is not typically used directly in fabrics but is processed further into DTY or FDY.
- DTY: A finished yarn with stable texture, high strength, and elasticity, ready for knitting or weaving.
C. DTY vs. Spun Yarn (e.g., Cotton):
- Spun Yarn (e.g., Cotton): Made from short, staple fibers twisted together. Known for natural feel, breathability, and absorbency. Can wrinkle easily and may lack durability compared to synthetics.
- DTY: A continuous filament synthetic yarn. Offers superior durability, wrinkle resistance, quick-drying properties, and consistent quality. Modern DTY can mimic the soft, bulky feel of spun yarns while retaining synthetic performance benefits.
VIII. Future Trends and Innovations in DTY Yarn
The DTY yarn industry is continuously evolving, driven by demands for sustainability, enhanced performance, and integration with advanced technologies.
A. Sustainability:
- Recycled DTY (RPET DTY): The use of recycled polyester from post-consumer plastic bottles is a major trend, significantly reducing reliance on virgin petroleum resources and lowering environmental impact.
- Bio-based DTY: Research and development are ongoing for DTY made from renewable bio-based polymers, further reducing the carbon footprint.
- Eco-friendly Manufacturing Processes: Innovations in dyeing, finishing, and texturizing processes aim to reduce water, energy, and chemical consumption.
B. Smart Textiles:
The integration of DTY with conductive materials and sensors is paving the way for smart textiles capable of monitoring vital signs, regulating temperature, or even generating power.
C. Enhanced Performance:
Continuous research focuses on developing DTY with even more advanced functional properties:
- Improved Moisture Wicking: Next-generation DTY yarns are engineered for superior moisture transport, enhancing comfort in high-performance activewear.
- Anti-microbial Properties: Yarns with inherent anti-microbial agents to inhibit odor-causing bacteria.
- UV Protection: DTY yarns designed to offer higher levels of UV protection for outdoor apparel.
D. New Texturizing Technologies:
Advances in texturizing machinery and techniques promise to create DTY with novel textures, enhanced bulk, and even more natural hand feels, pushing the boundaries of fabric design.
IX. Conclusion
Drawn Textured Yarn (DTY) has undeniably transformed the textile landscape, offering an unparalleled blend of comfort, performance, and versatility. From its meticulous manufacturing process, which imparts its unique bulk and elasticity, to its diverse applications spanning apparel, home textiles, and industrial uses, DTY has proven to be a truly indispensable material.
Its ability to mimic the softness of natural fibers while delivering the durability, wrinkle resistance, and easy-care properties of synthetics has made it a favorite among designers and consumers alike. As the industry moves towards a more sustainable and technologically advanced future, DTY continues to evolve, with innovations in recycling, bio-based materials, and smart textile integration promising to further expand its impact. DTY yarn is not just a fiber; it is a testament to textile engineering, continuously adapting to meet the dynamic needs of modern life and shaping the fabrics of tomorrow.